Since Roots blower operates continuously for a long time and the temperature rise of the motor body is too high, the bearing will not be dehydrated until the bearing is damaged, the shaft is bent and the belt is broken, which will lead to the stator and rotor. Friction (commonly referred to as broom) leads to a sharp rise in core temperature, insulation of combustion slot, turn to turn insulation, winding turn to turn short circuit or "shooting" on the ground. In severe cases, the stator core may be inverted, misaligned, the shaft may be worn, and the end cover may be scraped off.
Because long-term continuous operation of Roots blower will lead to high temperature rise of the motor itself, and the bearing is not filled with grease in time, which will lead to less bearing oil until the bearing is damaged, shaft bending, drive belt fracture and other conditions, resulting in friction between stator and motor rotor.
Not only Roots blower, but also bearings of other machines. When the bearing is damaged, unexpected equipment shutdown may be caused. Even if it is a one hour shutdown, the premature failure of bearings may cause huge production losses. To ensure the healthy operation of the equipment, in addition to relying on high-quality bearings, attention should also be paid to the operating environment, correct installation and regular maintenance.
When the bearings of Roots blower are replaced, new grease needs to be injected. There are certain requirements for the amount of grease. Too much is not good, and too little is not good. So how much is appropriate? Excessive use of lubricating grease will cause a lot of harm to bearings. Lubricating grease has a good effect on bearings, with good wear resistance, adhesion, temperature resistance, lubrication and rust resistance, which can improve high-temperature oxidation resistance, delay aging and dissolve carbon deposits. Prevent oil stain and metal debris from agglomeration, and improve the corrosion resistance, wear resistance and pressure resistance of machinery.
Correct installation and maintenance of Roots blower is an important factor to maximize the service life of bearings. At the same time, attention must be paid to the cleanliness of bearings, the correctness of bearing selection and the selection of appropriate installation and maintenance tools. In addition, the bearing must be protected from contamination by pollutants and moisture, and ensure correct installation and lubrication. In order to effectively ensure a more lasting service life of Roots blower.
1. The bearing is installed incorrectly. For example, the shaft is damaged due to the uneven tapping of the inner hole of the bearing during cold assembly, which results in the loss of interference between the inner hole of the bearing and the outer ring or the small mutual variation of the interference quality, resulting in the inner hole running condition. The motor end cover is installed by uneven tapping, which results in the loose matching between the end cover bearing chamber and the outer ring of the shaft, resulting in the outer ring running condition. No matter running the inner hole or going to the outer ring several times, the temperature of the bearing will rise significantly during operation. If the bearing is in good condition, it is allowed to run the outer ring intermittently.
2. The bearing wall of Roots blower is not cleaned or greased.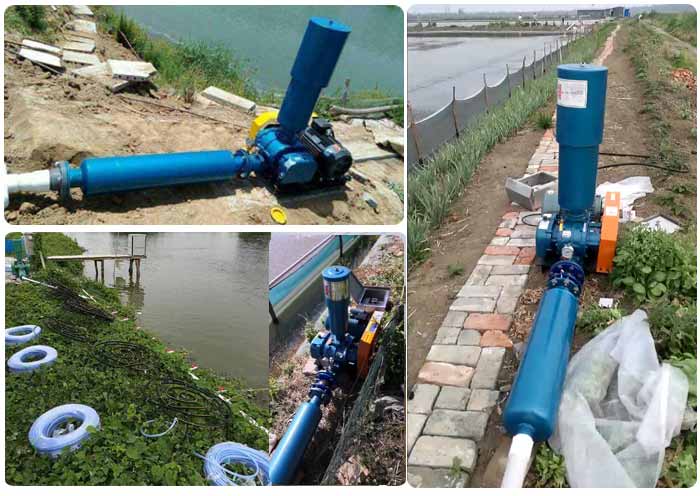
3. The bearing is replaced again for production and processing. After the motor end cover is nested and cycled, the clearance fit amount is large or the ovality is greater than the standard, which causes the side clearance of the bearing steel ball to be too small or uneven, which causes the sliding friction force to increase and the temperature to rise significantly until it is damaged.
4. Due to radial displacement of stator and motor rotor iron core or insufficient precision after machining the transmission shaft again, there is no cross section on the inner and outer rings of the bearing, resulting in high temperature after the bearing runs "hard to eat" until it is damaged.
5. The bearing is damaged due to the mutual use of grease with different models and specifications.
6. The bearing itself has product quality problems, such as rust on the raceway, unsmooth rotation, small side clearance, deformation of the ball bearing, etc.
7. The standby machine does not operate for a long time, the grease is mouldy, and the bearing is rusted. Only the maintenance and repair of the standby machine should be carried out in the application. Pay attention to the regular maintenance of the three leaf roots blower and the removal and replacement of the same grease on time.
I believe that after reading the above contents, you should also have a better understanding of the causes and solutions of the bearing damage of Roots blower. I hope it will be helpful to you.
Text label: Roots blower
Link to this article: //wuhanzhcs.com/html/news/n02/719.html